Ground loops for wired sensors
When working with wired sensors the cabling can greatly affect the signal. This means that a good sensor with bad cabling can create poor signals that distort the signal, making it impossible to analyze it accurately. Some of these more common issues include ground looping and electric interference.
Ground looping
Effective management of cable grounding is crucial to ensure robust shielding and prevent ground loops. Ground loops occur when a shared conductor, such as the signal return or shield, is connected to different points with varying electrical potentials creating a small current and causing unwanted interference.
In sensors using coaxial cables, the inner conductor carries both the signal and power, while the outer braid acts as shielding and provides a return path for the signal. Maintaining isolation between the shield and the sensor housing is essential to prevent ground loops. When using non-isolated sensors, employing an isolated mounting pad is recommended to mitigate these issues.
Figure 1: If isolated mounting pads are not used and there is a potential difference between the machine and instrument a ground loop is created which creates noise.
For sensors utilizing two-conductor shielded cables, one wire transmits the signal and power, while the other serves as the signal return. The cable’s shield protects against electromagnetic interference (EMI) and electrostatic discharge (ESD). Grounding the shield at a single point, typically at the readout equipment is critical. Proper grounding of cable shields is essential to protect sensor electronics from potential damage, especially in environments with elevated EMI and ESD levels.
Below are three examples of the difference between before and after an isolated mounting pad was installed. In the yellow spectra, most of the signal is lost, and the noise from the ground looping is mostly visible. In the blue spectra, an undistorted picture is visible.
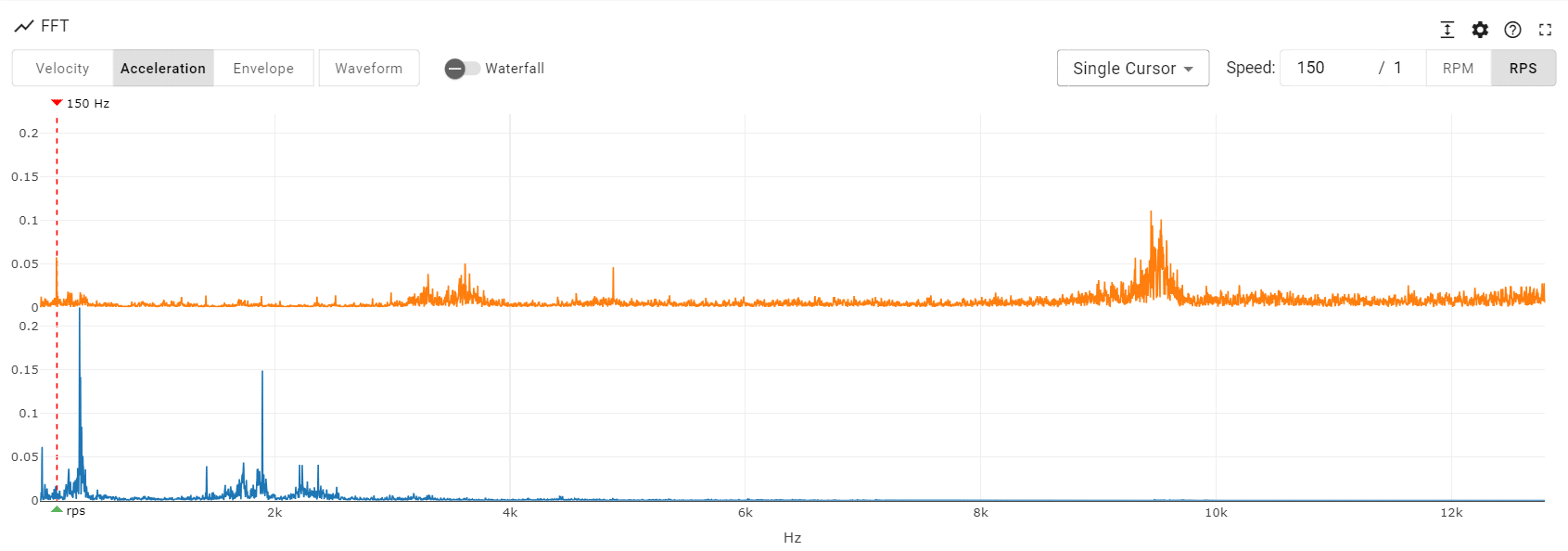
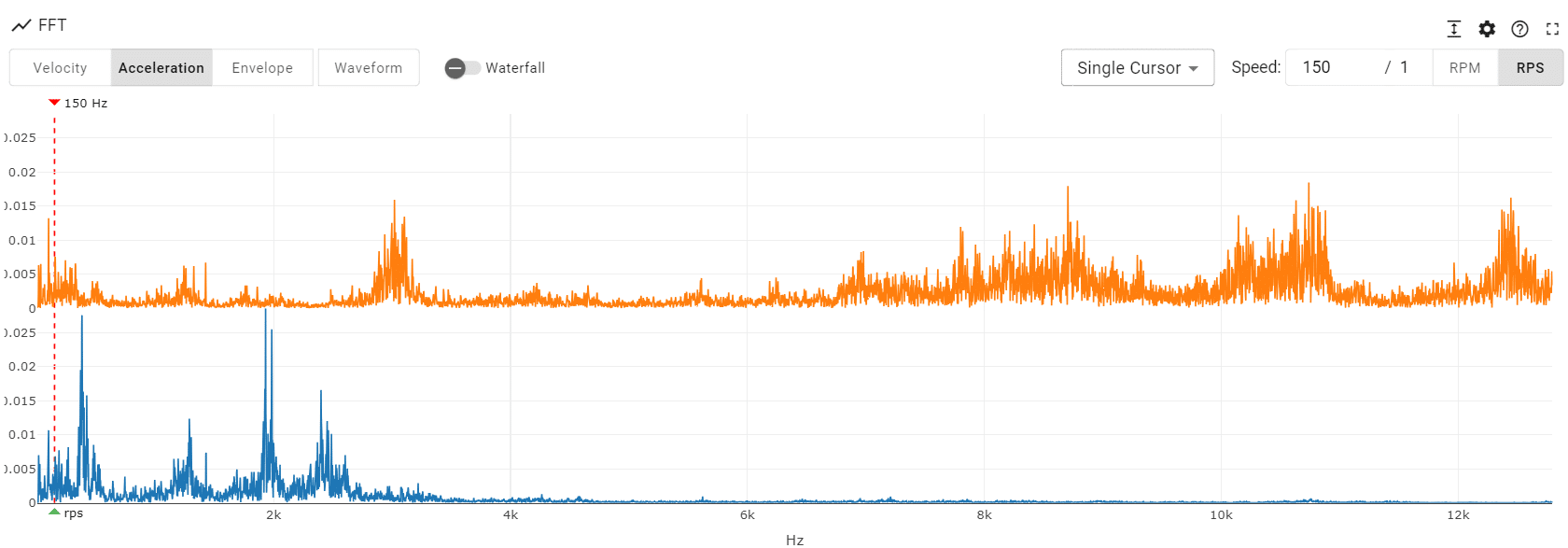
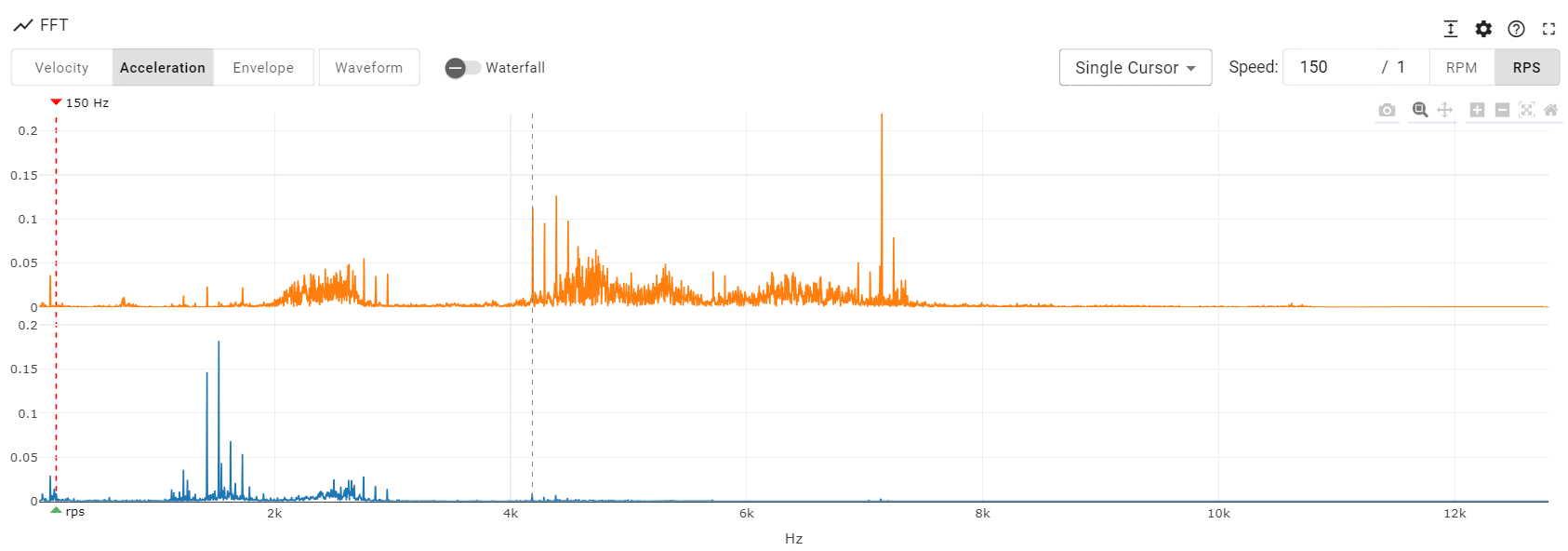
Electrical interference
Communication devices, power lines, and electrical discharges can all induce signal interference. To reduce errors caused by electromagnetic interference (EMI) and electrostatic discharge (ESD), it’s essential to use high-quality cables that are well-shielded. When splicing cables, ensure continuous shielding is maintained throughout.
Correctly routing cables is equally critical. Avoid placing sensor cables alongside AC power lines; if they must cross, do so perpendicularly. Whenever feasible, place sensor cables within a separate grounded conduit for added protection. Additionally, keep sensor cables clear of radio transmission equipment, electrical motors, generators, and transformers, as these can introduce interference. Minimize routing cables through areas prone to ESD. While sensors are typically safeguarded against ESD, severe cases can still briefly distort signals.
Conclusions
Following these guidelines can significantly reduce measurement errors and ensure more reliable sensor performance. There might be even more guidelines to follow to get the best results from your sensors. Make sure all of them are followed to ensure the best data quality, which will make it easier to achieve accurate analysis results for your machines.
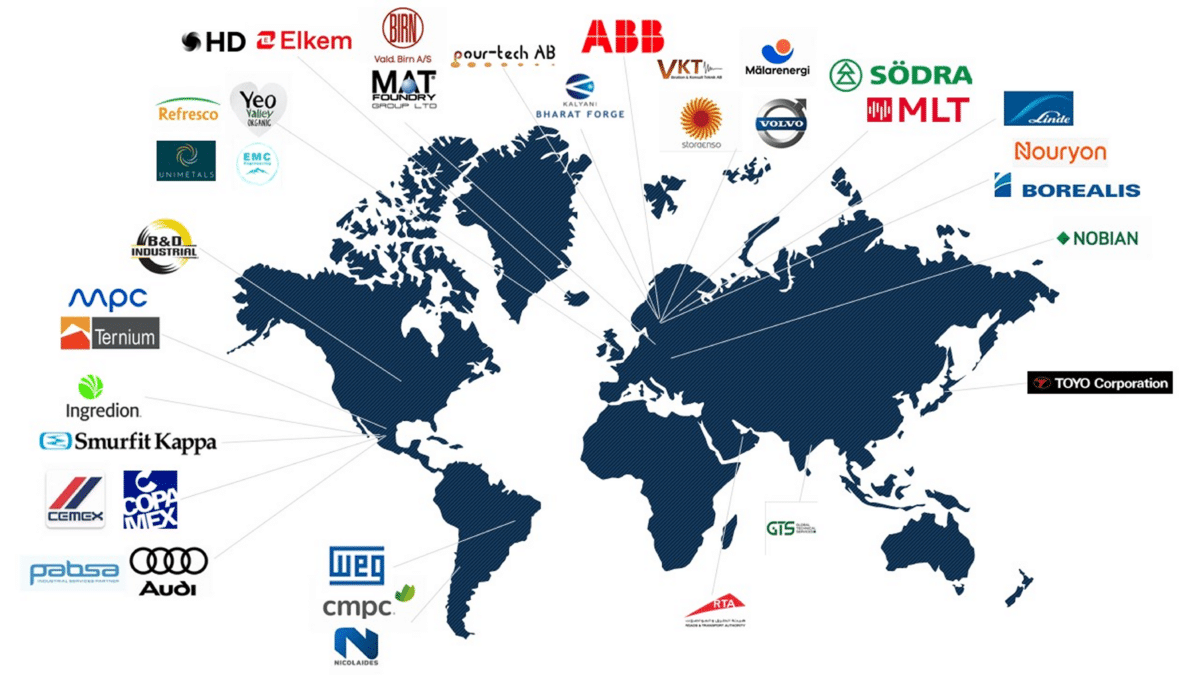