Mounting vibration sensor for condition monitoring
We have previously discussed how different settings (sample rate, duration, and dynamic range) affect sensor data and how wired sensor cabling can distort the collected signal. This is the last article in the series on data quality. It will touch on the last part important to the quality of the data collected: the sensor fitting.
Methods of fitting
To fit a sensor there are two different methods for permanent mounting, using adhesive or screwing it into the machine. There is also one method for temporary mounting, magnetic. Each method has its advantages and disadvantages, which we will explore here. In all cases, before installation, make sure that the surface is smooth, without any paint or dirt. Ensure the sensor is placed as close as possible to the vibration source.
Screwing
Many sensors have a threaded stud at the end. Using this by screwing it into the machine provides the best possible transmission to the sensors which enables monitoring of the widest possible frequency range (as long as the sensor supports it). The sensor must be torqued correctly. Under-torquing may lead to looseness, causing noise in the data, while over-torquing may damage the threads, sensor, or machine. It is advisable to apply some thread lock (Loctite 222 for example) to the threads during installation to prevent the sensor from unscrewing by the machine’s vibrations. Most sensors require a coupling fluid or coupling agent for the best transmission of high frequencies, please use what your sensor manufacturer prescribes for your sensors. Additionally, both disturbances cause changes in vibration metrics, making it harder to understand the machine’s development over time. Even a perfectly mounted sensor cannot provide accurate results above 30 kHz.
Adhesive
If drilling in the machine is not possible, adhesive mounting a disc and then screwing into the disc is the second best alternative not to damage the sensor. To make a good adhesive mount it is important to use the correct adhesive, many experts agree that epoxy or Loctite 454 is a good options that give good frequency responses. It is also important to keep the adhesive layer incredibly thin to not disturb the transmission of vibrations. Adhesive mounting cannot provide accurate results above 15 kHz.
Magnet
Using a magnet is an option mostly for handheld devices. However, this has a lot worse frequency response for high frequencies than a stud mount. If it should be used a completely flat, smooth, and ferromagnetic area close to the vibration source needs to be found. Magnet mounting will never yield good results over 10 kHz. However, this has improved over the last years with stronger magnets.
Mounting pads
Using a mounting pad is a clever option to get a good frequency response while still having the flexibility of using a magnet mount. Glue or screw the mounting pad to the machine and then stick the sensor to it by magnetic mounting. Since this option has a magnet both on the machine side and the sensor side the connection becomes significantly stronger and can therefore give a better frequency response than just using the sensor’s magnet to keep it to the machine.
Signs of poor fitting
The pictures below show the results of a sensor that was slowly loosened by the machine’s vibration over time. At the bottom, we see the blue spectra where we still see the machine vibration. Later the machine vibration disappears as the sensor gets looser and looser until the red where there is almost no signal left. The sensor is then reinstalled in the same place correctly and we see how the signal should look.
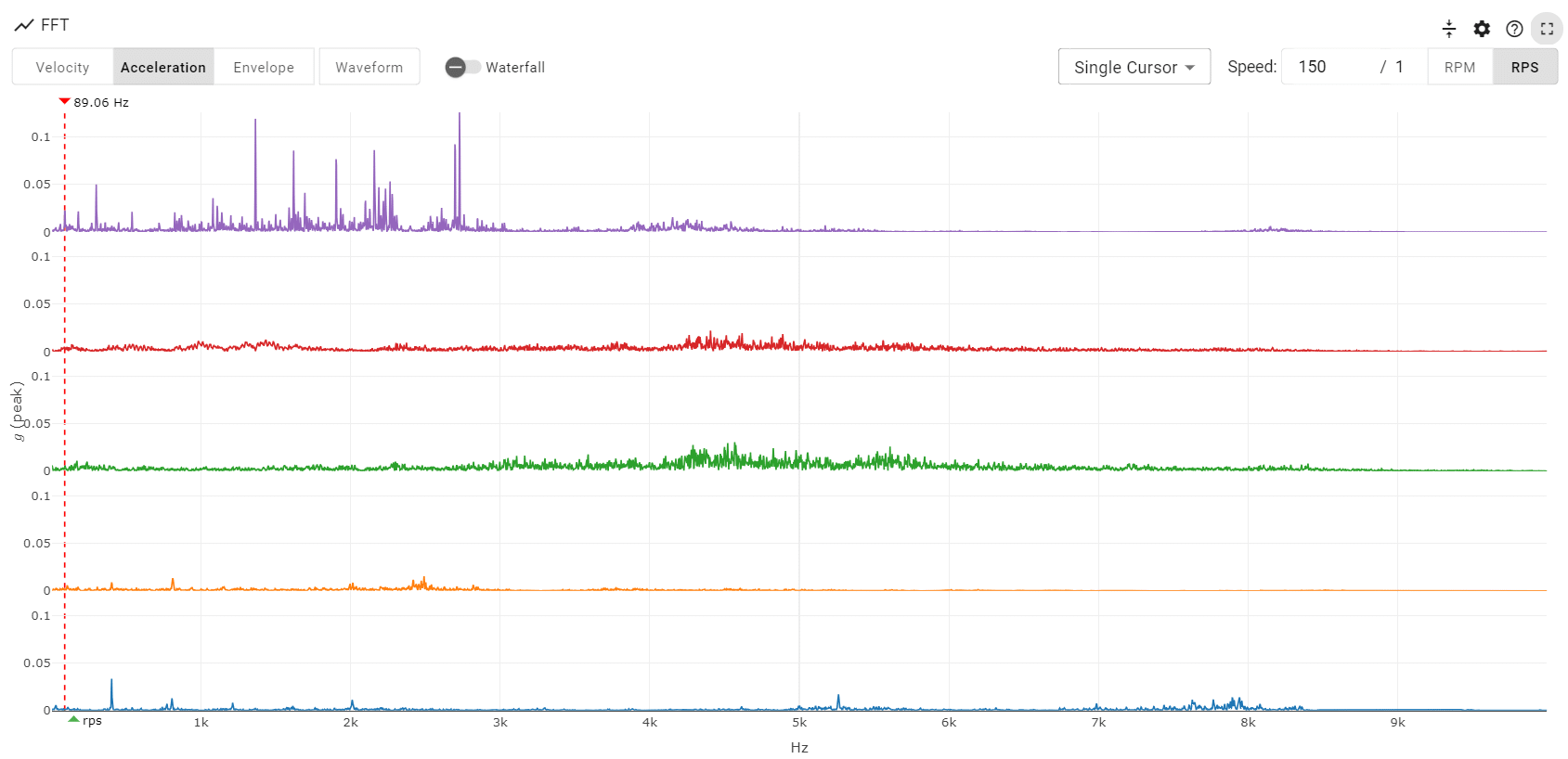
Bad mounting practice
There is in some ways the mounting position of the sensor can cause disturbances. For example, if the sensor is mounted on an irregularly moving element. Here are some examples:
This sensor are mounted on a surface that rotates 90 degrees periodically every 1.5 seconds. This results in low-frequency contributions to the spectra that make the signal harder to analyze.
This disturbance causes the vibration metrics to change, which makes it harder to understand the machine’s development over time. This would cause significant issues for a threshold method and is also unsuitable for MultiViz.
Conclusions
The mounting of sensors has a large impact on which frequencies are important. Magnet-mounted sensors cannot reliably capture signals over 5 kHz and should therefore not be used to collect data to produce spectra over 5 kHz. For optimal measurements, use stud-mounted or glued vibrational sensors or stud-mounted or glued magnetic mounting pads on smooth surfaces with the manufacturer-specified coupling fluid or agent.
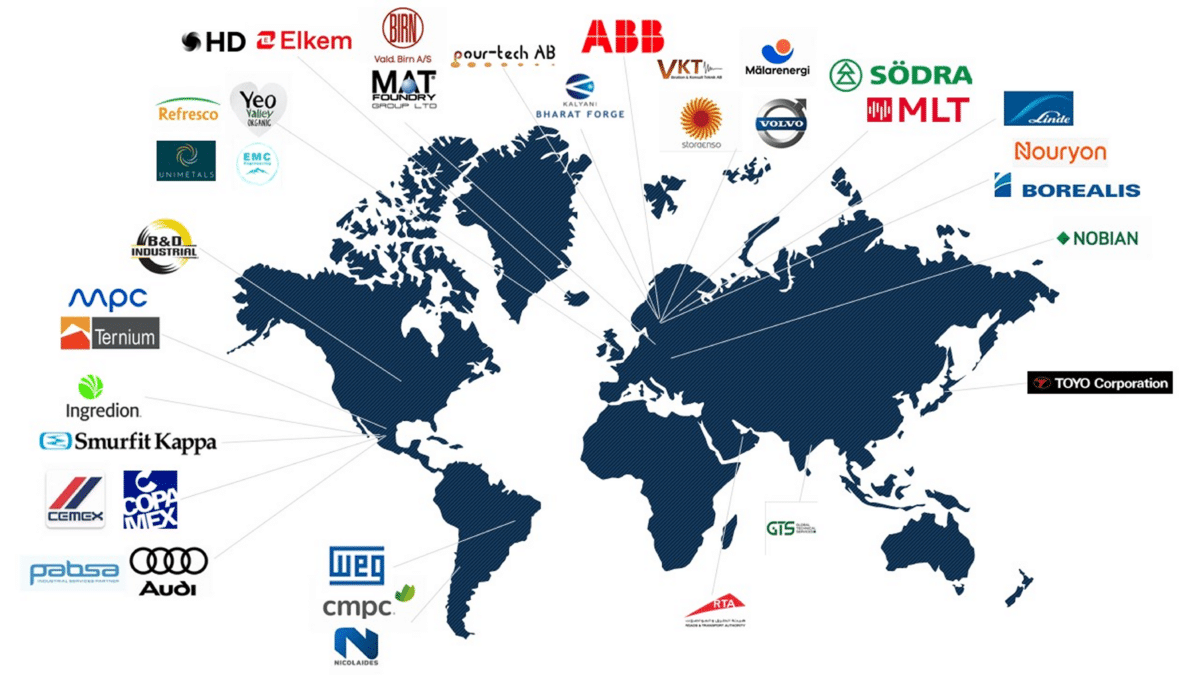